Why – A Lab for Hybrid People to do Great Work
We created Tomorrow Lab to give ourselves a place to create our dream projects. Ted and Pepin have hybrid backgrounds in design and engineering with deep interest and experience in science and technology.
We found there were many people just like us who sought to combine these interests. We call these designers and engineers Hybrid People. And in creating a place for these kinds of projects, we created a place for other Hybrid People to work and work with us.
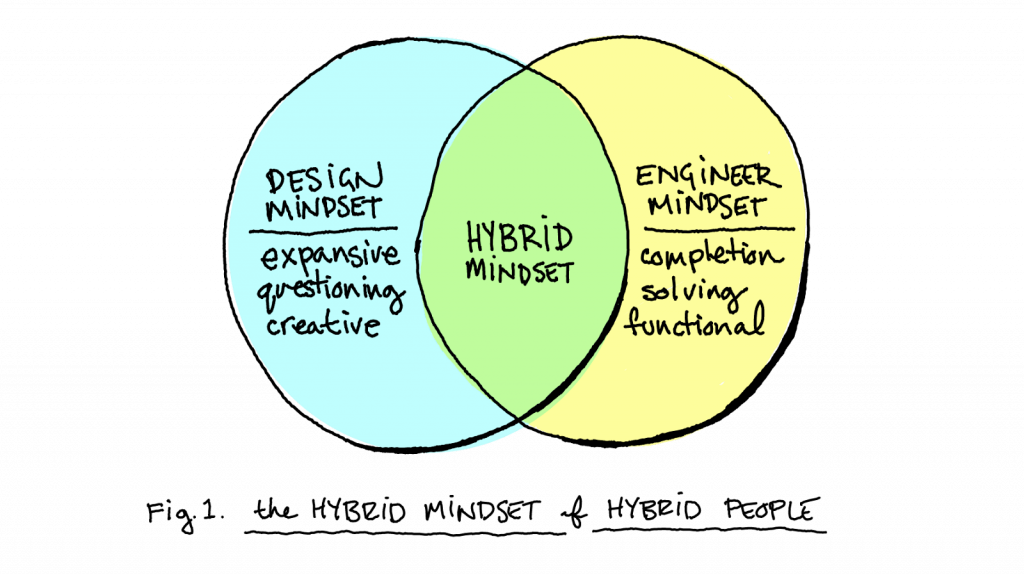
Hybrid people bring a mix of backgrounds to the table, and more importantly, they have experience with holding multiple concepts and perspectives in their heads simultaneously. This power leads to unparalleled insights that we believe cannot be produced any other way.
These insights lead to brilliant features, inventions and valuable IP for ourselves and our clients which, in turn, allow us to ask critical questions and solve important problems.
The Adheretech pill bottle from TL’s early work portfolio is a great example of a hybrid development approach. In that design we needed to create a sensor that could count pills inside a bottle using a capacitive measurement.
The solution also needed to be enjoyable and easy to use. Our team at the time consisted of experts with a blend of manufacturing, sensor design, electrical engineering, industrial design, user research and ergonomics.
The emerging design utilized a folded sensor layer that fit inside a long narrow sleeve. The solution bucked the form factor of a typical bottle in favor of a solution that made picking out pills very easy and vastly increased sensor accuracy.
How #1 – Holistic Innovation
It follows that a team of people with a hybrid mindset would, in turn, develop a process at the intersection of science and design. We found that IDEO’s Design Thinking process was ultra-focused on consumer needs without taking inspiration from the realm of the possible, and more specifically, the world of emerging technologies.
While we continue to see great innovation opportunities at the intersection of Feasibility, Viability and Desirability, we realized that designers and engineers needed to truly understand the materials they’re working with, and that technology was, indeed, a material to be understood and crafted with.
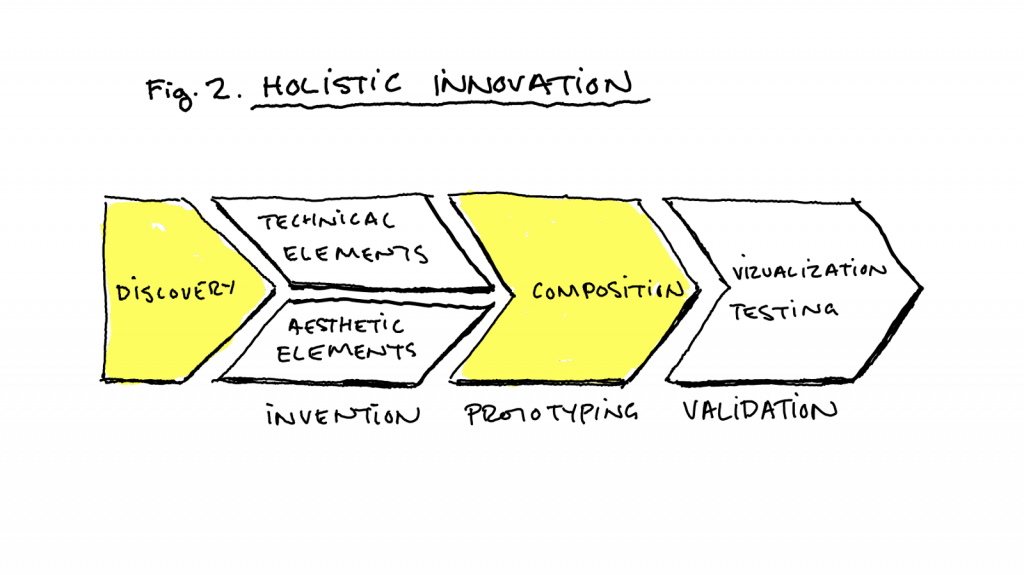
Our Holistic Innovation process blends Design Thinking and Technology Insights to invent new ideas and engineer the unique and detailed features that make a product great, delightful to use, and truly helpful. The Holistic Innovation process has four steps, culminating in a set of validated insights and a final product concept.
- Discovery – Investigate the User Story and Technology Landscape and Generate Insights and Product Concepts
- Invention – Isolate and Develop the Aesthetic and Technological Elements of the Product Concept
- Prototyping – Compose these Elements into a Prototype and a Detailed Product Vision
- Validation – Validate the Prototype with Key Stakeholders and Technical Feasibility Studies
This process is more than blending two exclusive concepts. Instead, it’s about getting deep inside the world of our users and the technological world they inhabit. Many components of the solution landscape and user experience depend heavily on what is at hand and what skills our users already have.
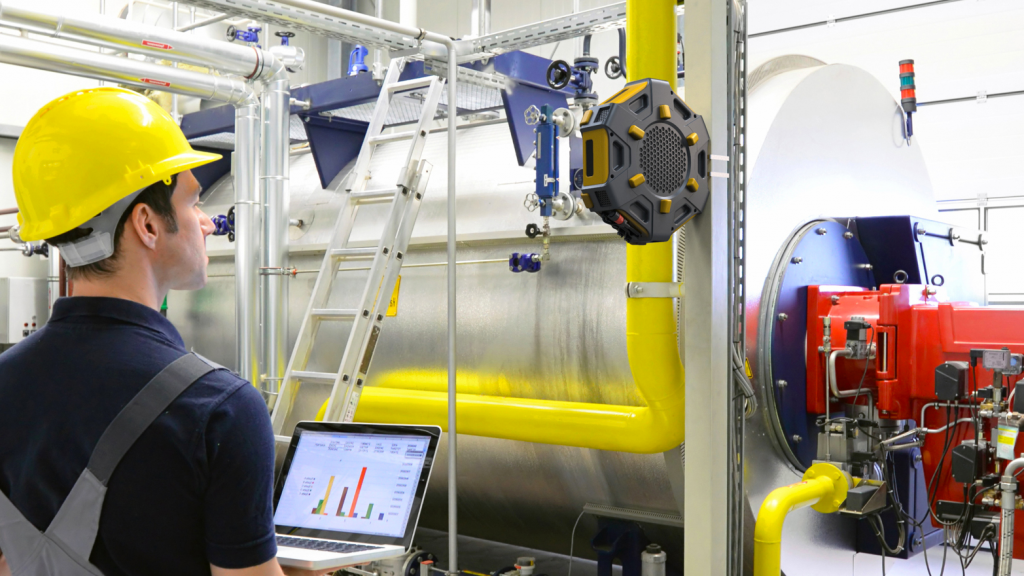
Holistic Innovation in Practice: Hivecell Case Study
This project we did for Hivecell is a great example of TL’s Holistic Innovation approach. In our initial design for the Hivecell we created a system of stackable supercomputers to empower edge computing and research application.
In the ruggedized version, we used our Holistic approach to understand the environmental, thermal, and resource constraints while still allowing for a skilled use-case and a high degree of versatility and expandability.
In just under 2 months of work, we developed a highly evolved, eye-catching design that was both functional and desirable.
How #2 – Co-invention
Great invention happens in a world with a wide range of inputs and it’s important for us to engage our clients as key players in that process. In our process we bring creative, design, and engineering skills to bear, but we cannot operate in a vacuum. We need co-inventors to supercharge, push-back, and guide our work.
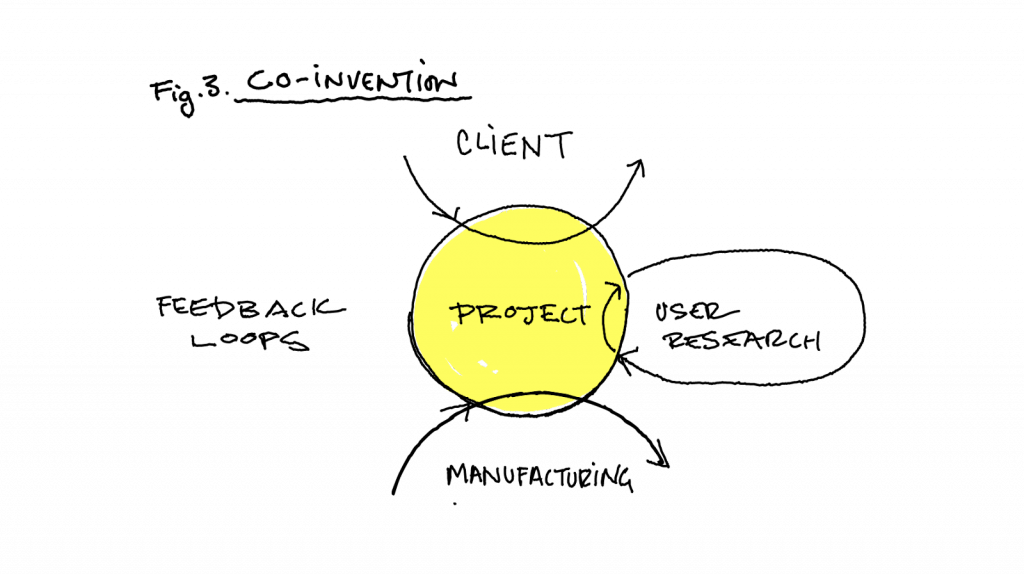
In our best work, three critical partners must engage with our process –
- User-Research – User Experience is the core of any good design today. Furthermore, deep user research is critical to providing the insights that identify and realize truly impactful features. We often have an unconventional approach to User Research, for many of our projects we “prototype first, ask questions later.” We believe you can ask a great research question, but you can learn much much more by putting a mock-up in a user’s hands.
- Client Partners – While user research guides our work and provides us with critical insights and validation, only a client can tell us if we’re on the right track. More often than not, we’re working with our client’s original IP and ideas. We’re also helping them realize their vision for a product. We provide ideas and realization, only a client can provide vision.
- Manufacturers – A great manufacturing team provides more than the means to bring a product to life – they provide engineering short-cuts, impressive background IP, and prototyping enhancements.
How #3 – Obsessive Prototyping
Good Design asks questions. But to get good answers you need to make a prototype — then you can ask even better questions. This kind of iteration makes the best products. They become more useful, more functional, more meaningful, and more beautiful with each cycle.
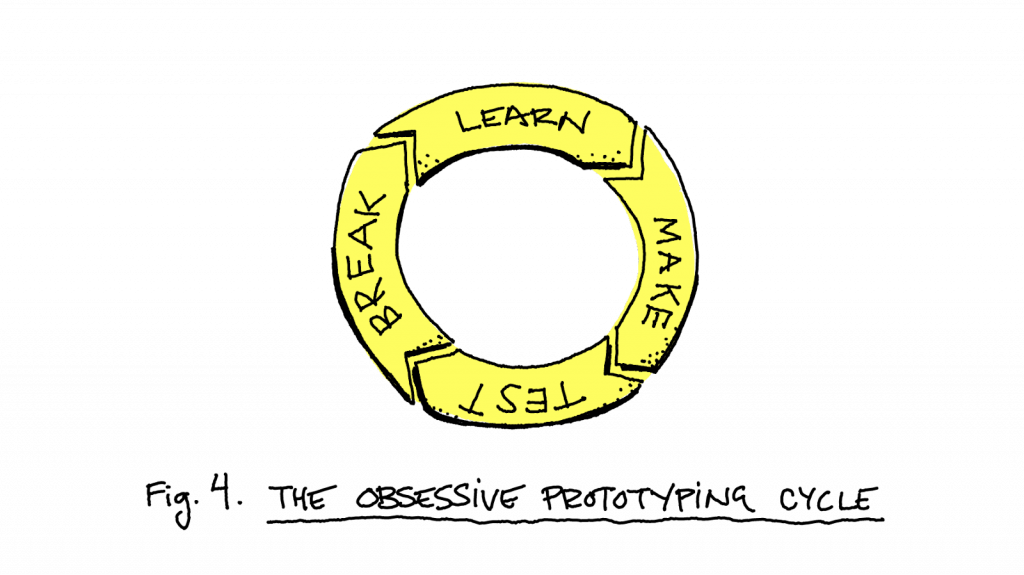
The steps in this cycle are:
- Learn – Start with a set of questions. Gather all of the insights required and form a hypothesis. Identify your constraints. Decide on the correct level of fidelity needed to answer your question.
- Make – Design a prototype that will answer your questions and test your hypothesis. In parallel, design the test or testing system. Fabricate at the required fidelity. Assemble.
- Test – Execute the test. Troubleshoot and modify the design to make it work and find pathways to further success.
- Break – Push the prototype to the limit to find it’s weaknesses and points of failure. It is tempting — especially for engineers — to make things work. It is also critical to make them fail.
- Repeat – Bring the insights from all four stages back to the Learning and repeat until all the co-creators and stakeholders are confident in the success and value of the design. The final prototype is the product sold at scale.
We obsess over prototyping – constantly exploring how we can use our tools and partners to make prototypes with incredible speeds and high fidelity. We’re also deeply practiced in creating the right type of prototype at the right time.
A messy, fast, mock-up can provide as much direction as a high-resolution 3D print. A reconfigurable breadboard can allow us to tune a mechanical design and ultimately reveal its suitability in a larger system. Lastly, only a truly experienced prototyping team can complete the integration that makes our work-like looks-like prototype so legendary.

In this project for Teralytic we developed dozens of rounds of prototypes. Early prototypes asked questions about sensors – each being prototyped and tested in an isolated container of soil.
Later prototypes tested the field readiness of the design, going so far as to injection mold housings and bring pre-production units into the field. Later prototypes refined the design for mass production and began testing the feasibility of removal, replaceable components that allowed us to refurbish and extend the lifespan of the product.
You can learn more about our stages of prototyping and testing in this post.
If you’re interested in working with Tomorrow Lab to invent a new product, prototype an idea, or develop your own holistic process, reach out here: http://tomorrow-lab.com/new-business
One response to “How We Work”
[…] our Holistic Innovation process we identified a series of Industrial Design form factors and User Experiences that could be […]
< Back to News